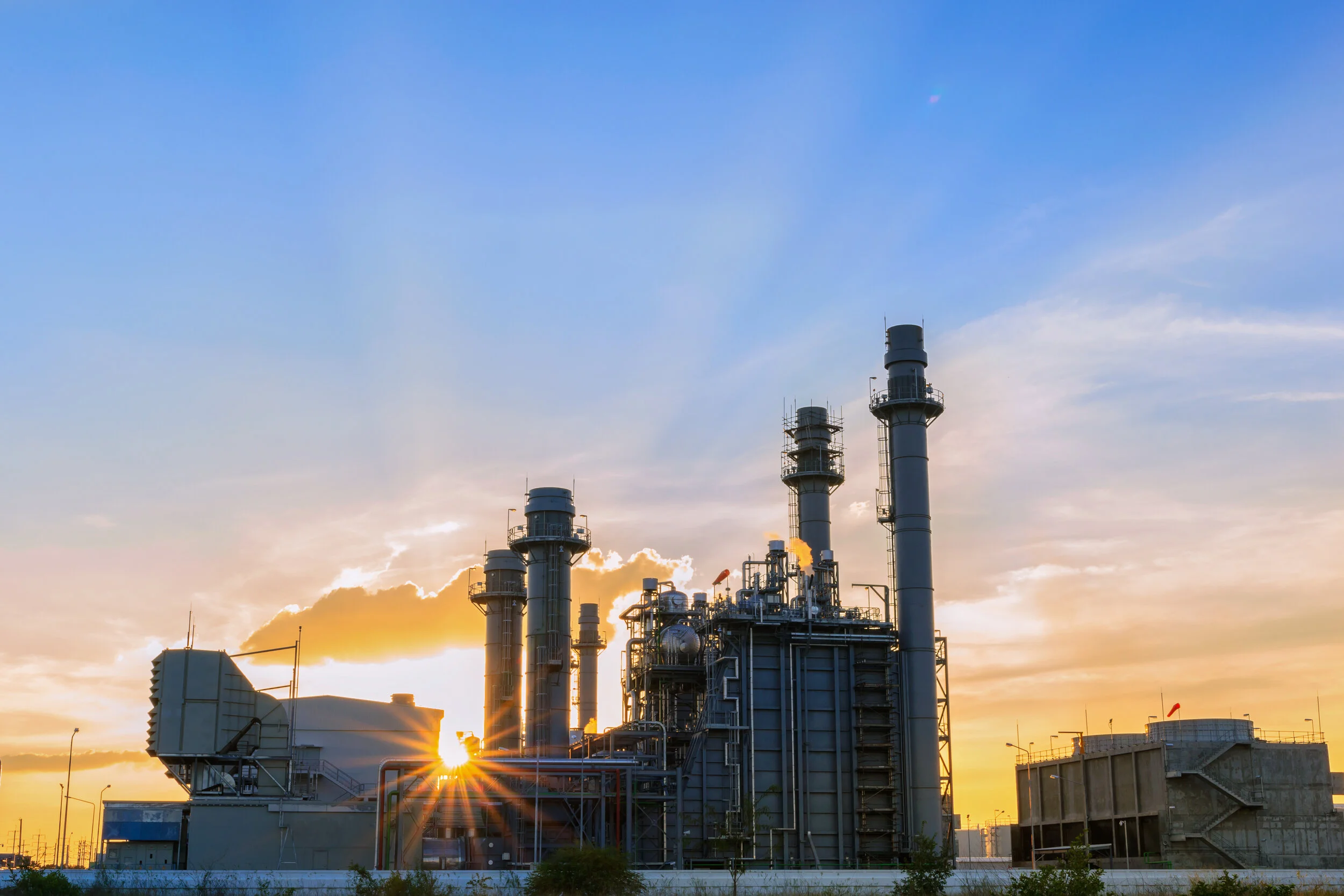
OPERATION & MAINTENANCE
Skilled Assistance. Full or Partial. On Demand
The equipment required to ensure maximum productivity is specialized, and highly technical. This is true for offshore and onshore oil and gas drilling, production, and gathering platforms, pipelines, oil terminals, refineries, natural gas processing, power generation, ports, marine bunkering, mining, cement plants, and others. No wonder it is equipment that Petrogas helps its clients operate and maintain (O&M).
Petrogas is an established O&M contractor with engineers and technicians fully trained and certified in plant or facility operation, maintenance, automation, process control, instrumentation, optimization, safety, and testing.
Best of all, we’re a complete solution, also able to handle pumps, valves, shutdowns, turnarounds, expansions, rehabilitation, improvement, modification, enhancement, retrofits and upgrades. Petrogas can even take over maintenance and servicing of your production-essential equipment (e.g., gas turbines, boilers, etc.)
We handle these tasks proactively, heading off issues before they become a production-halting breakdown, and ensure your operation remains online and profitable. We can also be counted on to respond quickly and decisively, getting you back to work ASAP. Indeed, several of our long-term O&M engagements began with an emergency call.
Bottom line: We can help you maintain and operate the most advanced equipment and streamline your O&M on a long-term basis and in an emergency capacity.
Contact us here to learn more.
The Best the World Has to Offer
Petrogas holds strategic partnerships with industry leaders in the United States and Europe. We leverage our select OEM and EPC relationships, local human resources, international expertise, operational scale, and geographical proximity to serve our African and Africa-based customers.
Petrogas primarily focuses on serving customers in the following industries/segments:
Upstream oil and gas exploration, drilling, and production onshore facilities and offshore platforms
Midstream gathering, processing, transportation, and storage of oil and gas
Downstream oil terminals, refineries, and petrochemical facilities
Power generation utilities
Ports and marine
Mining
Water and wastewater treatment plants
Asset Reliability, Condition Monitoring, and Predictive Maintenance
Petrogas provides a vast array of asset reliability, condition monitoring, and preventive maintenance services in the post-commissioning environment. Our solutions enable owners and operators to minimize operational risks, reduce running costs, and better focus on core business processes.
Some of our ongoing offerings include
Computerized Maintenance Management System (CMMS)
Equipment Installation
Maintenance
Upgrading of Existing Structures/Systems
Installation of Rotating Equipment
Commissioning
Start-up
Related Engineered Solutions
Working with us addresses key issues for the reliability of your plant and other critical factors.
Improve Equipment Availability
If your equipment is not reliable, the losses add up quickly. Routine maintenance can (and does) help, but it simply is not good enough to ensure availability. Routine maintenance does not reveal the emerging health issues in your critical assets that can result in unit shutdowns/slowdowns. Servicing needs to be proactive, which is what we provide.
Wasted Maintenance
Maintenance practices are often driven by time and original equipment manufacturer (OEM) recommendations rather than actual asset condition. Limited insight into the condition of equipment health can result in unplanned failures, expensive repairs, and lost production. Again, we go beyond OEM and deliver true maintenance solutions that keep equipment running (as opposed to simply checking a box).
Reactive Maintenance
The oldest maintenance approach is reactive (or "run-to-failure"), which essentially means that the equipment isn't repaired or replaced until it breaks. The issues here become obvious:
Costly downtime. Equipment fails with little or no warning, so your operations grid to a halt until replacement parts arrive, resulting in lost revenue.
Higher maintenance costs. Unexpected failures can increase your labor costs (i.e., paying overtime rates), as well as expedited delivery of replacement parts.
Safety hazards. Unexpected equipment failure could create a safety issue with the failing equipment or other units that might be affected.
Reactive maintenance can be appropriate in some circumstances, such as for non-critical and low-cost equipment with little or no risk of collateral damage or lost production. To give a small but clear example, it makes little sense to change a common light bulb before it burns out. It is important, however, to make sure that any failure will not create a chain reaction that affects more critical equipment.
Petrogas, with its global partners, delivers integrated solutions that ensure you a seamless trouble-free operation.